In the pulsating heart of industrial innovation, where speed marries accuracy and efficiency dances with reliability, CNC servo presses have emerged as the unsung heroes of modern manufacturing. These machines aren’t just tools—they’re game-changers, reshaping how industries approach stamping, forming, and assembly processes. Let’s dive into why these high-performance systems are transforming factories worldwide—and how they could revolutionize *your* production line.
---
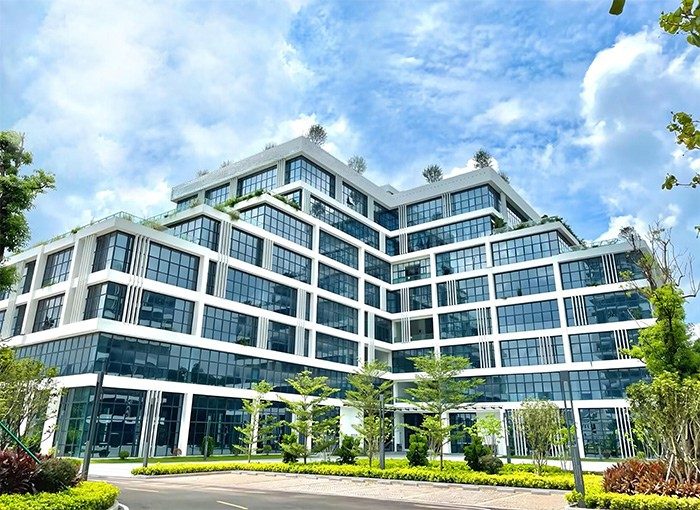
### THE EVOLUTION OF PRESS TECHNOLOGY: FROM BRUTE FORCE TO BRAINPOWER
Gone are the days of clunky mechanical presses roaring like dinosaurs on the factory floor. Traditional hydraulic and pneumatic systems, while effective for their time, often operated with the subtlety of a sledgehammer. Enter CNC servo presses: intelligent, adaptive, and precise. By integrating servo motor technology with computerized controls, these systems deliver unparalleled control over force, speed, and position—down to micrometer-level accuracy.
Imagine a press that “thinks” as it works:
- Adjusting pressure in real-time to accommodate material variations
- Learning optimal paths for complex forming operations
- Slashing energy use by up to 60% compared to legacy systems
This isn’t sci-fi—it’s today’s manufacturing reality.
---
### WHY INDUSTRY LEADERS ARE MAKING THE SWITCH 🌟
1. **Precision That Pays Dividends**
In aerospace component manufacturing, where a single flawed rivet can ground an entire aircraft, servo presses maintain tolerances tighter than a Swiss watch. Medical device producers leverage this accuracy for implantable components where 0.01mm deviations matter more than ever.
2. **Flexibility Without Compromise**
Automotive suppliers juggling 20 different part designs? No problem. With programmable stroke profiles and quick die-change systems, servo presses switch jobs faster than a Formula 1 pit crew. Tesla’s Gigafactories reportedly reduced changeover times by 75% after adoption.
3. **Energy Efficiency That Boosts ROI**
Traditional presses waste energy like a leaky bucket. Servo systems only consume power during active pressing phases, with regenerative braking actually putting energy back into the grid. One German automaker reported €380,000 annual savings per press—numbers even CFOs can’t ignore.
---
### REAL-WORLD APPLICATIONS MAKING WAVES 🌊
**Case Study 1: Electric Vehicle Battery Production**
A leading EV manufacturer struggled with lithium-ion cell stacking consistency. After implementing 200-ton CNC servo presses with AI-driven pressure monitoring:
- Defect rates plummeted from 8% to 0.3%
- Production speed increased by 40%
- Thermal runaway incidents during compression dropped to zero
**Case Study 2: Micro-Electronics Assembly**
When a smartphone maker needed to place 0.2mm connectors without cracking delicate PCBs, servo presses delivered:
- 99.998% placement accuracy
- 50% reduction in rejected boards
- Ability to handle 8 different component types in one cycle
---
### FUTURE-FOCUSED FEATURES DRIVING TOMORROW’S INNOVATION 🔮
The latest servo press advancements read like a tech wishlist:
- IoT integration for predictive maintenance
- Machine learning algorithms optimizing tool paths
- Hybrid systems combining additive and subtractive processes
- Haptic feedback interfaces letting operators “feel” the forming process
Industry 4.0 isn’t coming—it’s here, and servo presses are its backbone. Early adopters in the semiconductor sector are already using these features to achieve what was impossible just three years ago.
---
### OVERCOMING IMPLEMENTATION CHALLENGES 🛠️
Transitioning to servo technology isn’t without hurdles:
- **Skill Gaps**: Training programs blending CNC programming with materials science
- **Initial Costs**: Creative financing models like press-as-a-service arrangements
- **Legacy Integration**: Smart retrofitting kits breathing new life into old presses
Companies that navigate these challenges successfully often find the payoff exceeds their wildest projections. One Midwest auto parts supplier tripled their contract bids within 18 months of upgrading.
---
### YOUR COMPETITORS AREN’T SLEEPING—ARE YOU? ⏰
While you read this, factories across 14 time zones are installing servo presses to:
- Cut production costs by 22-35%
- Reduce scrap material by up to 90%
- Achieve ISO 9001 compliance with automated quality logs
- Slash carbon footprints through energy recovery systems
The question isn’t “Can we afford to upgrade?” but “Can we afford NOT to?”
---
### MAKING THE LEAP: FIRST STEPS TO SERVO SUCCESS 🏆
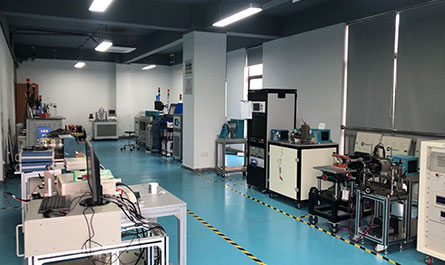
1. **Audit Current Processes**: Identify high-error or energy-intensive operations
2. **Partner with Experts**: Look for integrators with cross-industry experience
3. **Start Small**: Pilot a single press for your most problematic line
4. **Measure Religiously**: Track OEE, energy use, and defect rates pre/post implementation
Remember—the goal isn’t just new equipment, but transformed manufacturing DNA.
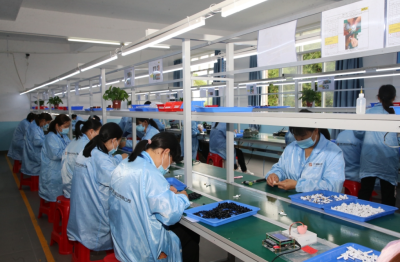
---
### CONCLUSION: PRESSING INTO A SMARTER FUTURE 🔋
CNC servo presses aren’t merely machines—they’re manufacturing philosophers, constantly asking:
“Can we do it better? Faster? Cleaner?” In dynamometer where sustainability meets hyper-competition, these systems offer more than technical specs—they provide a competitive soul.
The factories of tomorrow won’t be judged by their size, but by their intelligence. Where does yours stand?
[END OF CONTENT]
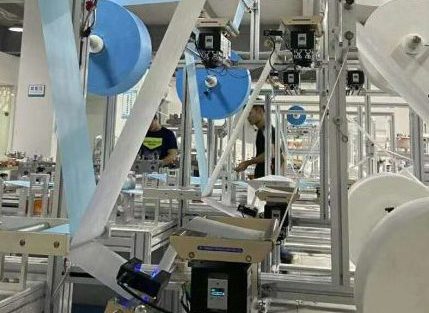